- Product Info
- SUMIKAEXCEL PES
- Powder Use
SUMIKAEXCEL PES powder applications
Features of SUMIKAEXCEL PES powder
SUMIKAEXCEL PES powder grades are suitable for the following applications:
- Dissolve in a solvent and use as an adhesive, paint, or coating agent
- Dissolve in a solvent and process into hollow fiber membranes or cast membranes (flat membranes)
- SUMIKAEXCEL PES-based compounds and epoxy reinforcement
The following powder grades are available:
Table 7-1 SUMIKAEXCEL PES powder grades
Powder Grade | RV (reduced viscosity) * | Main Use |
---|---|---|
3600P | 0.36 | Compound |
4100P | 0.41 | Paints, coatings, adhesives |
4800P | 0.48 | Hollow fiber membrane, adhesive |
5003PS | 0.50 | Paints and coatings, adhesives, epoxy reinforcements |
5200P | 0.52 | Hollow fiber membrane |
5900P | 0.59 | Hollow fiber membrane |
7600P | 0.76 | Hollow fiber membrane |
* Reduced viscosity is measured in a 1% solution in dimethylformamide (DMF).
Table 7-2 SUMIKAEXCEL PES grade lineup
Reduced Viscosity | 0.36 | 0.41 | 0.48 | 0.52 | 0.59 | 0.76 | ||
---|---|---|---|---|---|---|---|---|
Powder | 3600P | 4100P | 4800P | 5200P | 5900P | 7600P | ||
5003PS * | ||||||||
Pellet | Non-reinforced | 3600G | 4100G | 4800G | ||||
Glass fiber reinforced | 3601GL20 | 4101GL20 | ||||||
3601GL30 | 4101GL30 |
* Grade containing hydroxyl group (OH group) at the terminal end
Physical properties of SUMIKAEXCEL Powder Grade
Properties of SUMIKAEXCEL 3600P, 4100P, and 4800P
The physical properties of the powder types 3600P, 4100P, and 4800P are equivalent to those of the pellet types 3600G, 4100G, and 4800G.
Table 7-3 Physical properties of 3600G, 4100G, and 4800G
Test Method | unit | 3600G/4100G/4800G | ||
---|---|---|---|---|
General physical properties | Density | ISO 1183 | g/cm3 | 1.37 |
Mold shrinkage (MD) | Sumitomo Chemical Method | % | 0.60 | |
Mold shrinkage (TD) | Sumitomo Chemical Method | % | 0.60 | |
Water absorption rate (23℃, 24hr) | ISO 62 | % | 1.0 | |
Mechanical properties | Tensile strength | ISO 527-1,2 | MPa | 85 |
Tensile Yield Strain | ISO 527-1,2 | % | 6.5 | |
Bending strength | ISO 178 | MPa | 130 | |
Flexural modulus | ISO 178 | MPa | 2,600 | |
Izod impact strength (unnotched) | ISO 180/1U | kJ/m2 | Not complete break | |
Izod impact strength (notched) | ISO 180/1A | kJ/m2 | 8 | |
Rockwell hardness (M scale) | ISO 2039-2 | - | 95 | |
Thermal properties | Deflection temperature under load (0.45MPa) | ISO 75 | ℃ | 214 |
Deflection temperature under load (1.80MPa) | ISO 75 | ℃ | 205 | |
Linear expansion coefficient (MD) | ISO 11359-1,2 | 10-5 /K | 5.5 | |
Linear expansion coefficient (TD) | ISO 11359-1,2 | 10-5 /K | 5.5 | |
Electrical properties | Dielectric constant (absolutely dry: 100Hz) | IEC 62631-2-1 | - | 3.5 |
Dielectric constant (absolute temperature: 1MHz) | IEC 62631-2-1 | - | 3.4 | |
Dielectric constant (absolute temperature: 1GHz) | IEC 60250 | - | 3.4 | |
Dielectric tangent (absolute temperature: 100Hz) | IEC 62631-2-1 | - | 0.002 | |
Dielectric tangent (absolute temperature: 1MHz) | IEC 62631-2-1 | - | 0.004 | |
Dielectric tangent (absolute temperature: 1GHz) | IEC 60250 | - | 0.004 | |
Volume resistivity | IEC 62631-3-1 | Ω m | >1013 | |
Dielectric breakdown strength (1mm) | IEC 60243-1 | kV/mm | 43 | |
Tracking resistance | IEC 60112 | V | 150 | |
Combustion quality | Flame Retardant Classification | IEC 60695-11-10 | - | VO |
Limiting oxygen index (1.6mm) | ASTM D2863 | % | 38 |
Properties of SUMIKAEXCEL 5003P and 5003PS
- It is an amorphous resin with a glass transition point of 230°C.
- It has good adhesive properties due to the large number of terminal hydroxyl groups (0.6 to 1.4 per 100 polymer repeat units).
- Other properties are equivalent to other grades of SUMIKAEXCEL PES.
Paints and Coatings
SUMIKAEXCEL 4100P and 5003PS are used in the paint and coating field. 5003PS in particular is a grade that has enhanced heat hardness, chemical resistance, and adhesion to metals.
This article describes paints and coatings that use SUMIKAEXCEL 5003PS.
Features of paints and coating agents using SUMIKAEXCEL 5003PS
- It is stable even when used for long periods at 250°C in air, or during thermal cycles (0°C⇔250°C).
- Adhesive properties and bonding: Exhibits excellent adhesion to glass, ceramics, iron, stainless steel, aluminum, and aluminum alloys.
- Solvent resistance: Among amorphous resins, it exhibits excellent solvent resistance.
- Hydrolysis resistance: Polyethersulfone resin itself is a resin with excellent hydrolysis resistance, and 5003PS exhibits even better hydrolysis resistance.
- Good film-forming properties: Excellent film-forming properties provide sufficient protection for the substrate.
- Flame retardant: Highly flame retardant without the addition of flame retardants.
- Transparency: It has excellent transparency and retains the original appearance of the base material even after coating.
- Hygienic: It is hygienic as it does not contain additives such as plasticizers.
How to apply SUMIKAEXCEL 5003PS (Example of solution method)
- The substrate is degreased and, if necessary, blasted or etched.
- Dissolve SUMIKAEXCEL 5003PS in the solvent.
- The solution is applied to the substrate by dipping, brushing, spraying, etc. and allowed to air dry for 20 minutes.
- The mixture is baked at 350-400°C in air for 30 minutes.
Prevents gelation
SUMIKAEXCEL PES solution may gel, which is explained as a crystallization involving both the PES molecules and the solvent.
(Features)
- The solution may become cloudy and solidify entirely.
- Once a gel is formed, it is difficult to redissolve it even if a solvent is added.
- The gel acts as a nucleus for gelling the ungelled solution.
- When heated, it melts and returns to its original solution.
(Prevention of gelation)
- Do not apply excessive shear stress. Avoid using homogenizers.
- Do not leave at high concentrations for long periods of time. Do not leave swollen PES in unstirred solvent.
- A mixture of solvents is recommended.
Concentration-viscosity correlation
The concentration-viscosity correlation of SUMIKAEXCEL 4100P and 5003PS in NMP solutions is as follows:
Figure 7-1 Concentration-viscosity correlation of SUMIKAEXCEL 4100P and 5003PS in NMP solution
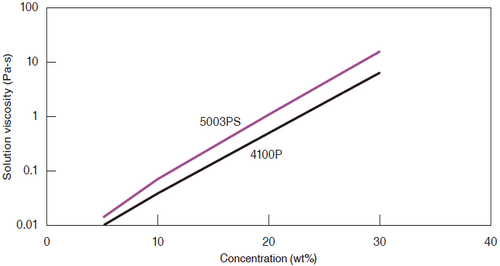
Heat resistance of SUMIKAEXCEL 5003PS coating on aluminum plate (example)
Table 7-4 Continuous heat resistance (250℃ in air)
Evaluation item | Time (hr) | ||
---|---|---|---|
0 | 115 | 235 | |
Appearance changes | - | no change | no change |
Grid test *1 | 100/100 | 100/100 | 100/100 |
Corrosion resistance test *2 | No corrosion | No corrosion | No corrosion |
Table 7-5. Thermal cycle test (2 minutes in 0°C ice water and 2 minutes in 250°C air)
Evaluation item | Number of cycles (times) | ||
---|---|---|---|
0 | 25 | 50 | |
Appearance changes | - | Almost no change | Slight foaming at edges |
Grid test *1 | 100/100 | 100/100 | 100/100 |
Corrosion resistance test *2 | No corrosion | No corrosion | No corrosion |
*1 SUMIKAEXCEL 5003PS coating layer was scored with a safety razor in a 1mm x 1mm cross-cut pattern over an area of 100mm2 all the way down to the substrate, then cellophane adhesive tape was pressed against it and the layer was peeled off to count the number of SUMIKAEXCEL PES pieces remaining on the substrate.
*2 A 15 vol% sulfuric acid solution was dropped onto the SUMIKAEXCEL 5003PS coated surface, a glass plate was placed on top, and the surface was left for 24 hours before observing the changes in the surface.
For epoxy-based reinforcement systems
SUMIKAEXCEL 5003PS has been used for epoxy reinforced systems. The advantages of using 5003PS are as follows:
- Increases the fracture strength of the epoxy.
- It has a very high Tg.
- It has excellent mechanical properties.
Toughening of epoxy resin
SUMIKAEXCEL 5003PS is inherently tough, with a high Tg and modulus, which allows it to add toughness to epoxies without compromising the overall system performance. As shown in the table below, it has a significant breaking strength (GI C) and Tg does not decrease significantly.
Table 7-6 Effect on TGDDM/4,4-DDS system
5003PS concentration (%) | Flexural modulus (GPa) | Tg(℃) | GIC(kJ/m2) |
---|---|---|---|
0 | 3.34 | 205 | 0.28 |
10 | 3.21 | 205 | 0.41 |
15 | 3.07 | 200 | 0.47 |
(Note)
1) GICis measured under plane strain conditions at -65℃.
2) Tg was measured by torsional DMA
Comparative study results for epoxy resin/As4CF system with polymer concentration of 30wt%
Table 7-7 Comparison of SUMIKAEXCEL PES and PEI
Evaluation item | unit | P.E.I. | 5003PS | |
---|---|---|---|---|
CAI(Compressive After Impact strength) | MPa | 194 | 223 | |
Compressive strength | (room temperature) | MPa | 1697 | 1731 |
(82℃) | 7434 | 1648 | ||
(82℃)/Wet | N/A | 1076 | ||
Viscosity at 88℃ (Pa・s) | 130 | 100 |
N/A: No analytical data available
Application of SUMIKAEXCEL PES to aircraft and sporting goods fields
Thermosetting epoxy resin is used as the matrix resin in CFRP (a composite material made of carbon fiber and resin).
Epoxy resins have excellent mechanical and thermal properties, but are more brittle than thermoplastic resins. For use in the aircraft and sporting goods fields, improving fracture toughness (Compressive After Impact strength: CAI) is essential. By adding 5003P, it reacts with the epoxy resin and provides high toughness against impact fracture accompanied by delamination in the matrix resin.
How to use SUMIKAEXCEL PES
5003P is dissolved in an epoxy base material to make a homogeneous system. When a curing agent is added to this and cured, it reacts with the hydroxyl groups of 5003P to form a special morphology of an island structure, improving impact resistance. To dissolve 5003P in an epoxy base material to obtain a homogeneous system, there are two methods: 1) finely grinding 5003P and dissolving it directly in the epoxy base material at about 150°C under a N2 atmosphere, or 2) homogeneously dissolving the epoxy base material and 5003P in a solvent, and then distilling off the solvent to obtain a homogeneous system.
SUMIKAEXCEL PES usage per unit composite (example)
- Per unit matrix resin
Epoxy base (100 parts): Hardener (30-40 parts): 5003P (30 parts) - Per unit prepreg
~10wt%
Use in aircraft construction
When actually using it as a structural material for aircraft, etc., if the surface of the CF prepreg prepared using the above-mentioned method for using SUMIKAEXCEL 5003P is sprinkled with 5003P particle size-adjusted particles (Tough balls) and several dozen sheets are laminated and molded, the impact resistance will be further improved by the PES balls at the interface.
There are many different methods for stacking.
(Example: Boeing's standards for aircraft structural materials)
- CAI (Compressive After Impact strength) value is 310MPa or more
- CS (Compressive Strength. Hot/Wet Condition) value is 1100MPa (82℃) or more
Adhesive Applications
SUMIKAEXCEL PES can be used as a heat-resistant adhesive. It has excellent adhesive strength, especially when bonding metals together.
Features
- The adhesive layer has high tensile shear adhesive strength and T-peel adhesive strength, and exhibits well-balanced properties that combine rigidity and flexibility.
- It has the highest heat resistance of any thermoplastic resin adhesive on the market, and even at 200°C, its practical tensile breaking adhesive strength is extremely high at 20 MPa.
It can also be used repeatedly at temperatures up to 250°C for short periods of time. - It has excellent chemical and heat resistance.
- It contains no solvents or volatile components and provides excellent adhesion without a primer to a wide range of materials including aluminum, stainless steel, steel and brass.
Adhesion Method
Hot melt adhesive method using SUMIKAEXCEL PES film
- Cut the film to the size of the substrate.
- If necessary, roughen the surface of the substrate with sandpaper or a disc sander, etc., and clean with acetone, toluene, etc.
- Sandwich the film between the adherends, lightly press them together using a jig, and heat at 300-360°C for 10-30 minutes. The degree of pressing is sufficient so that the molten resin comes out as a small flash between the adherends.
- Allowing it to cool will result in a strong bond.
Adhesive method using adhesive solution
SUMIKAEXCEL 5003PS solvent system
When 5003PS is dissolved in a single solvent, it is unstable and PES precipitates, so a mixed solvent system is usually used. (In a single solvent, the solution stability is low and gelation occurs.)
Table 7-8 Examples of mixed solvent systems for SUMIKAEXCEL 5003PS
solvent | solvent | Mixing ratio (volume ratio) |
---|---|---|
A | Dimethylformamide Cyclohexanone Methyl Ethyl Ketone |
20 80 25 |
B | N-Methyl-2-pyrrolidone Toluene or xylene |
2 1 |
C | N-Methyl-2-pyrrolidone Toluene or xylene Silicone Flow Regulator Methyl Ethyl Ketone |
60 30 0.5~1 35 |
D | Sulfolane γ-Butyrolactone |
1 1 |
E | Sulfolane Acetone or methyl ethyl ketone |
1 1 |
Adhesion Method
The adhesive strength of PES adhesive changes depending on the heat treatment conditions, so it is necessary to set conditions according to how it is used.
(Example condition 1) Dry at 130℃ for 2 hours
(Example condition 2) 100℃, 1 hour, then dry at 350℃ for 15 minutes
Properties of SUMIKAEXCEL 5003PS adhesive system
It has excellent adhesive strength at high temperatures. For example, when 18-8 stainless steel is bonded to another piece of stainless steel using SUMIKAEXCEL 5003PS adhesive, the change in adhesive strength when the temperature is raised to 220°C and the adhesive strength retention rate when aged at 150°C are shown in Tables 7-9 and 7-10.
Table 7-9 Effect of temperature on peel strength
Temperature (℃) | Peel strength (MPa) |
---|---|
23 | 37 |
150 | 26 |
220 | 14 |
The peel strength was measured at a peel speed of 12.5 mm/min.
Table 7-10 Effect of peel strength and high temperature retention time
Holding time at 150℃ (hr) | Peel strength at 150℃ (MPa) |
---|---|
0 | 26 |
1000 | 21 |
Even after being held at 150°C for 1000 hours, it retains 81% of its initial adhesive strength.
PES membrane filter cartridge filter (Courtesy of Toyo Roshi Co., Ltd.)
This cartridge filter is made of a PES membrane filter and polypropylene and has excellent chemical and heat resistance.
Features
- Almost no substances are eluted, so only a small amount of cartridge washing is required as pretreatment.
- The media is asymmetrical and a pre-membrane filter with different pore sizes is built in, providing high efficiency, high flow rate, and a long filtration life.
- Autoclave sterilization and in-line steam sterilization are possible.
- The media itself is inert, so there is little adsorption of sample components.
Applications
- Ultrapure water microfiltration in electronics.
- Particle removal and sterilization filtration of process gases and vent air.
Figure 7-2
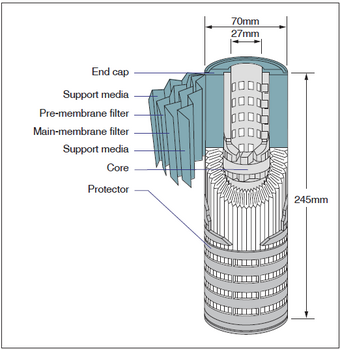