- Product Info
- SUMIKASUPER ™ LCP
- Welding of LCP
Welding of SUMIKASUPER ™ LCP
Welding of LCP
From the viewpoint of durability and weld strength, SUMIKASUPER LCP is often joined by welding, the most representative of which are hot plate welding, vibration welding, and ultrasonic welding. In recent years, laser welding, which uses laser light, has also become popular.
When welding SUMIKASUPER LCP, the resin temperature, shear (vibration) and other conditions during welding are very important. Ultrasonic welding and CVT (IR + vibration welding) as shown in the table below are suitable for welding SUMIKASUPER LCP.
Table 5-1-1 Representative welding methods for SUMIKASUPER LCP
Welding Method | Hot plate welding | Ultrasonic Welding | Vibration Welding | Laser welding | IR welding | CVT welding (IR+Vibration Welding) |
|
---|---|---|---|---|---|---|---|
Application to SUMIKASUPER LCP | × Melting point Because it is expensive Does not melt |
○ | × Melting point Because it is expensive Does not melt |
△~× If the product is thick Laser Not transparent |
△ | ○ | |
Weldability | Welding Strength | Compatibility range Limited |
○ (Small items are good) | ◎ | ◎ | ○ | ◎ |
Appearance of the welded part | △ | ○ | ○ | ◎ | ◎ | ◎ | |
Weldable resin | Thermoplastic resin |
Thermoplastic resin |
Thermoplastic resin |
Transparent Resin Absorbent resin |
Thermoplastic resin |
Thermoplastic resin |
|
Welding Time | ×× | 0.1 to 5 seconds | 2 to 10 seconds | 2 to 15 seconds | 10 to 30 seconds | 5 to 30 seconds | |
Weldable size | Heater Size dependence |
Business card size | Pallet Size | Tail Lights degree |
Instrument panel size | Instrument panel size | |
Design | Product shape restrictions | Heater shape limit |
fundamentally flat |
3D Shape | High degree of freedom | Vibration welding Excellent |
High degree of freedom |
Welding Design | Exclusive Design | Exclusive Design | Exclusive Design | Exclusive Design | Exclusive Design | Exclusive Design |
Ultrasonic welding
Ultrasonic welding is a method of joining surfaces by melting them through frictional heat using ultrasonic waves (20 to 40 kHz). Each grade of SUMIKASUPER LCP can be welded using ultrasonic vibration. The strength of the bonded surfaces remains almost unchanged even after heat aging at 250°C for one hour.
Shear strength test method
-
Figure 5-2-1 Ultrasonic welding test method
Unit: mm
The test conditions are as follows:
- Test specimen
12.7×78×1.6mm test pieces x 2
(One of the test pieces has the protrusion shown in the right figure.) - Welding Method
After setting the test piece as shown in the right figure, vibration was applied for 0.6 to 0.8 seconds under the conditions of a frequency of 19.5 kHz, an amplitude of 34 μm, and a load of 176.4 N. - Shear strength measurement
Tensile speed 1.67×10-4 Measure the shear strength in m/s.
Table 5-2-1 Weldability with ultrasonic welder (unit: N)
Shear strength (N) | ||
---|---|---|
After welding | 250℃, 1hr Thermal aging |
|
E5008L | 650 | 570 |
E5008 | 510 | 400 |
E4008 | 460 | 460 |
E6008 | 740 | 740 |
E6006L | 710 | 650 |
Infrared (IR) Welding
Infrared (IR) welding is a new technology that heats and joins plastic parts without contact. Since infrared rays are irradiated only on the joints, other parts are not affected by the heat, resulting in a beautiful finish. While ultrasonic welding and vibration welding, which use vibration, can cause problems with scratches, infrared welding uses non-contact heating and does not cause scratches. SUMIKASUPER LCP can be infrared welded.
Figure 5-3-1 SUMIKASUPER LCP IR welding test method
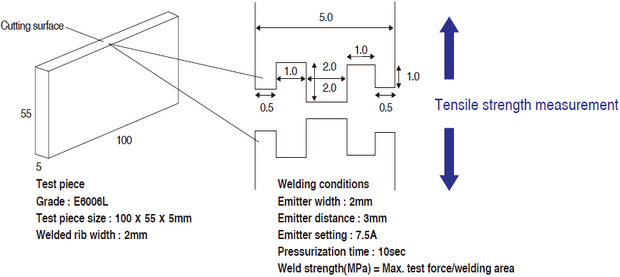
Table 5-3-1 IR adhesive strength of SUMIKASUPER LCP
IR exposure time (s) | Pressure (MPa) | Penetration (mm) | Welding strength (MPa) |
---|---|---|---|
40 | 1.5 | 1.2 | 13.2 |
50 | 1.5 | 1.5 | 12.8 |
50 | 3 | 1.8 | 13.1 |
CVT (IR+vibration) welding
SUMIKASUPER LCP cannot be welded by vibration welding because sufficient heat is not generated, but it can be welded by heating it with IR beforehand and then vibration welding. This allows for larger molded products than ultrasonic welding. If you want to increase the weld strength, we recommend CVT (IR + vibration) welding.
Figure 5-4-1 Test method for CVT welding of SUMIKASUPER LCP
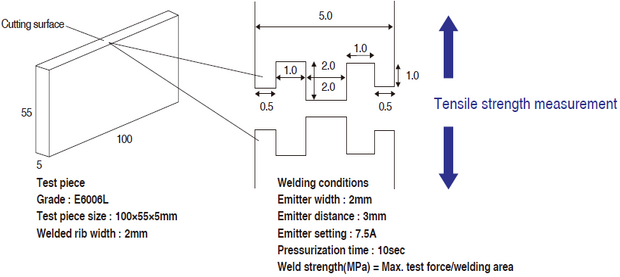
Figure 5-4-2 CVT adhesive strength of SUMIKASUPER LCP
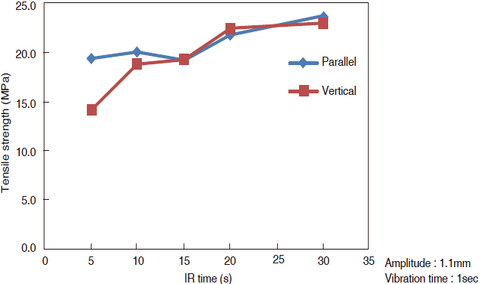
Laser welding
Laser welding is a method of welding by irradiating a laser beam and generating heat at the interface with the object. Laser resin welding combines a "light-transmitting resin" and a "light-absorbing resin." SUMIKASUPER LCP can be laser welded, but please note the following points.
<Transmitting side material>
SUMIKASUPER LCP is highly filled with filler, so it has low laser (infrared) transmittance, and so the thickness of the molded product must be thin. Molded products that can be laser welded must be 0.3 mm or less thick (please consult with our staff for thicknesses over 0.3 mm). The infrared transmittance is low at 10-30%, so the range of conditions is narrow. For LCP that can be laser welded, grades with a small amount of filler are suitable, and grades that use only glass fiber are ideal. Grades that contain inorganic fillers are not very suitable because they have low transmittance.
<Absorption side material>
Use the same black grade as the transparent side material.
Figure 5-5-1 SUMIKASUPER LCP laser welding test method
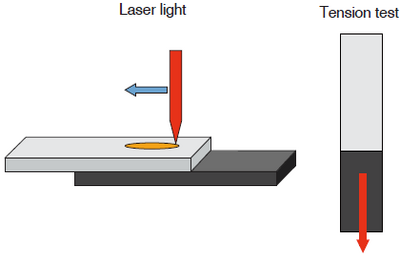
Table 5-5-1 Laser welding strength of SUMIKASUPER LCP
Transmitting side | Absorption side | Glass plate | Welding strength (MPa) | ||
---|---|---|---|---|---|
Grade | Test piece thickness | Grade | Test piece thickness | ||
E6008 | 0.3mm | E6008 B | 0.5mm | Not used | 8.6 |
E6008 | 0.3mm | E6008 B | 0.5mm | Used | 10.2 |
E4008 | 0.3mm | E4008 B | 0.5mm | Not used | 10.1 |
E6007LHF | 0.3mm | E4008 B | 0.5mm | Not used | 15.6 |